プレスリリースなど
ナノカーボンデバイス研究センターのプレスリリース等はこちら2022年
電流密度、寿命を飛躍的に改善し、大容量のリチウム金属電極を実現
-リチウムデンドライトを抑制する、カーボンナノチューブ負極部材を開発-
ナノチューブ実用化研究センターと日本ゼオン株式会社は共同で、スーパーグロース単層カーボンナノチューブ (SGCNT) を用いて作製したシートにより、リチウム金属の充放電時に発生するデンドライト(樹枝状結晶)を抑制する技術を開発しました。
2021年
室温で量子輸送可能な2.8 nmのカーボンナノチューブトランジスタ
-熱・応力誘起らせん構造転移による金属CNT内半導体ナノチャネルの実現-
国立研究開発法人物質・材料研究機構(NIMS)を中心とする国際共同研究チームは、透過型電子顕微鏡(TEM)内高精度ナノマニピュレーション技術の開発を行い、個々のカーボンナノチューブ(CNT)に対して局所的にらせん構造を変化させ、金属-半導体転移を制御することにより、CNT分子内トランジスタの作製に成功しました。
人工知能により材料の構造画像を生成し、物性を予測する技術を開発
-AI技術で扱える材料を広げ、材料開発加速へ-
・今まで物性を予測することが難しかった材料に利活用可能なAI技術を開発
・カーボンナノチューブのような複雑な構造をもつ材料のAI画像を生成し、物性を高精度に予測
・材料選定・加工・評価といった一連の工程をコンピューター上の仮想実験で再現
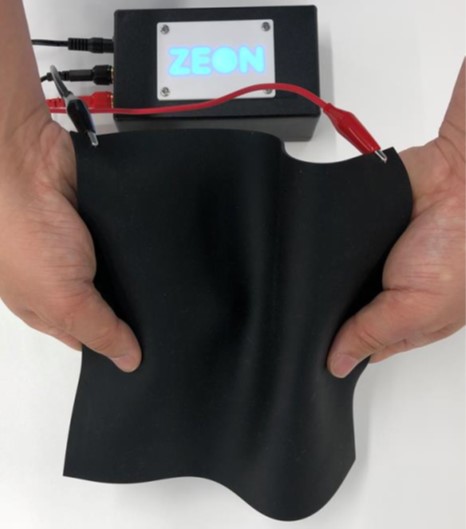
丈夫で柔軟なCNTシリコーンゴム複合材料を開発
-導電性ゴムとして医療用ウェアラブル機器の電極パッドに実用化-
ナノチューブ実用化研究センターと日本ゼオン株式会社は共同で、CNTの効果的な添加により高導電性を付与し、神経調節療法用医療機器の電極パッド等に適応可能な導電性シリコーンゴム複合化材料を開発しました。
2020年

熱や衝撃に強い多層カーボンナノチューブ樹脂複合材料を開発
-カーボンナノチューブが均一な導電性と高い形状保持性も付与-
ナノチューブ実用化研究センターとサンアロー株式会社は共同で、樹脂母材と同等の衝撃強度(靭性)を維持したまま、高温でのより優れた機械的強度や高い形状保持性、均一な導電性を付与したスーパーエンジニアリングプラスチック ポリエーテルエーテルケトン(PEEK)と多層カーボンナノチューブ(CNT)の複合材料を開発しました。
2019年
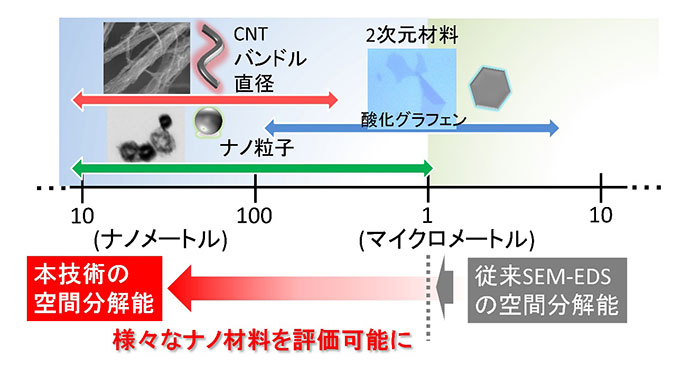
走査型電子顕微鏡での元素組成分析を高い空間分解能で実現
カーボンナノチューブの表面官能基の均一性を微細構造レベルでイメージング
走査型電子顕微鏡(SEM)中でのエネルギー分散型エックス線分光法(EDS)による元素分析を従来よりも2桁以上高い空間分解能で可視化する技術を開発しました。
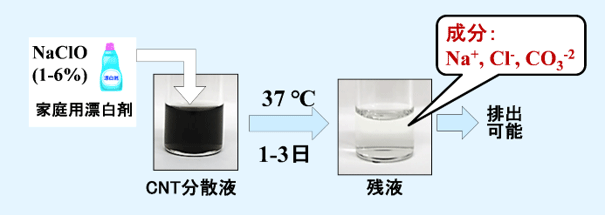
次亜塩素酸化合物によるカーボンナノチューブ廃水の工業的処理法の開発
安全・安心なカーボンナノチューブの産業化に貢献
カーボンナノチューブ(CNT)と次亜塩素酸化合物との化学反応を利用し、CNTを含む産業排水から簡便で効果的にCNTを除去する方法を開発しました。
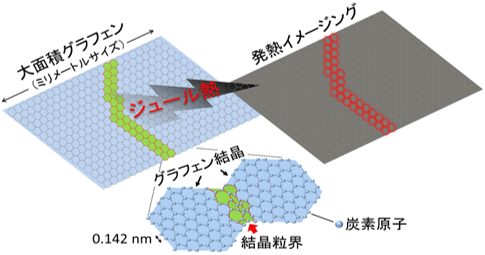
大面積グラフェンのさまざまな欠陥構造を高速・高精度に可視化する技術
ロックイン赤外線発熱解析法による二次元層状物質の新しい評価技術
微弱信号を高効率に検出できるロックイン赤外線発熱解析法を用いて大面積グラフェン膜のさまざまな微細な欠陥構造を高速・高精度で可視化できるイメージング評価技術を開発しました。
2018年
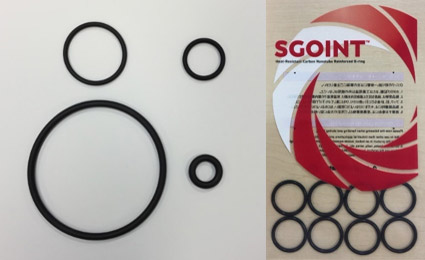
長寿命・高耐熱・高耐圧Oリングを開発、販売開始へ
世界初、スーパーグロース法で量産された単層CNT応用製品
ナノチューブ実用化研究センターと日本ゼオン・サンアロー・産総研CNT複合材料研究拠点(TACC)は、新エネルギー・産業技術総合開発機構(NEDO)のプロジェクトの成果をもとに長寿命・高耐熱・高耐圧のOリングの実用化に成功しました。2018年10月1日からサンアロー(株)が「SGOINT(スゴイン)-Oリング」の名称で販売を開始します。このOリングは高品質で大量合成に向くスーパーグロース法で量産された単層CNT(SGCNT)を応用した世界初の製品となります。
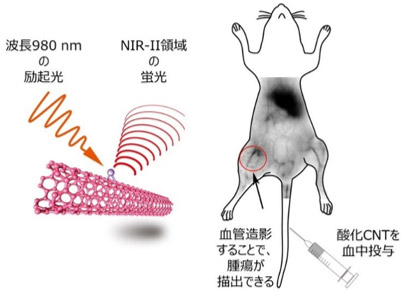
酸化カーボンナノチューブを用いた高輝度近赤外蛍光イメージングプローブ
簡便に効率良くCNTを酸化する手法を開発
近赤外領域で蛍光を発する酸化カーボンナノチューブ(CNT)の高効率・簡便な合成法を開発しました。本手法による酸化CNTを用いた近赤外蛍光イメージングプローブを作製し、その有効性をマウスの血管造影で実証しました。
2017年
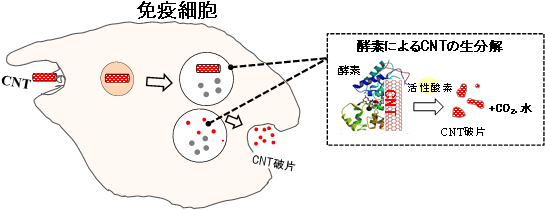
スーパーグロース単層CNTの生分解性を確認
免疫細胞内CNT生分解率の測定技術を開発
カーボンナノチューブ(CNT)の細胞への取り込み量を近赤外光吸収測定法を用いて定量評価し、スーパーグロース単層CNTSGCNTが生分解されることを発見しました。SGCNTが生分解されることで活性酸素発生量が減少し、細胞への毒性が低下することが示唆されました。
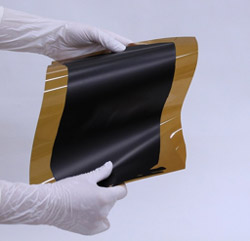
カーボンナノチューブを用いた塗料で電磁波遮蔽
多様な基材に、過酷環境でも使える電磁波遮蔽塗布膜を実現
カーボンナノチューブ(CNT)を用いた水性塗料で、99.9 %以上の電磁波遮蔽能を持つ塗布膜を実現しました。高い耐熱性と優れた長期安定性を備え、さらに曲げに強く、複雑な形状部や可動部でも使用が可能です。自動車用ワイヤーハーネスやロボットなど、多様な分野での電磁波遮蔽対策への活用が期待できます。
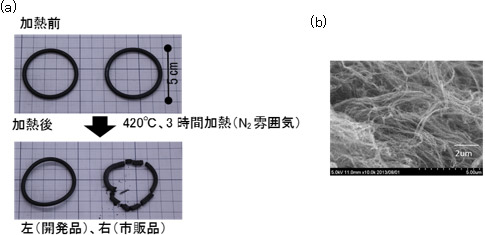
高温でも形状を維持できる強靭で安全性の高いOリングを開発
CNTとの複合化で耐熱性を向上
カーボンナノチューブ(CNT)とフッ素ゴムを複合化したOリングを開発しました。CNTの持つ繊維の補強効果により、通常フッ素ゴムが熱劣化する高温でも形状を維持することが可能です。自動車・化学プラントなど、高温・高圧耐性が要求される過酷環境下へ用途を拡大が期待されます。
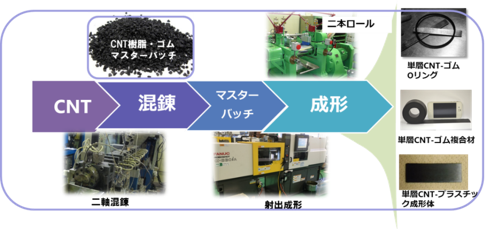
「日本ゼオン・サンアロー・産総研CNT複合材料研究拠点」を設立
本格的に実用化が迫る単層CNT製品産業を加速
産業技術総合研究所(産総研)は、産総研の技術を民間へ効率的に橋渡しするために、日本ゼオン(株)、サンアロー(株)と、「日本ゼオン・サンアロー・産総研CNT複合材料研究拠点」(TACC)を設立して研究を展開することで合意しました。
2016年
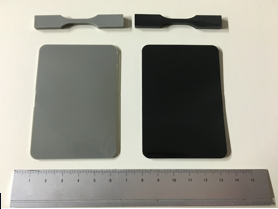
スーパーエンジニアリングプラスチック
「PEEK/SGCNT複合材料を開発」
単層CNT添加で世界最高水準の耐熱性と機械強度を達成
単層CNT融合新材料研究開発機構(TASC)と産業技術総合研究所は、スーパーエンジニアリングプラスチックの一種であるポリエーテルエーテルケトン(PEEK)にスーパーグロース法で作製した単層カーボンナノチューブ(SGCNT)を加えることで、世界最高水準の耐熱性と機械強度を同時に達成し、かつ射出成形可能な新しいスーパーエンジニアリングプラスチック「PEEK/SGCNT複合材料」を開発しました。
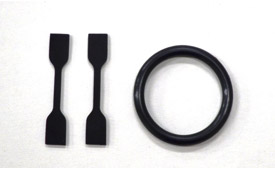
世界最高水準の耐環境特性ゴム材料を開発
単層CNT添加で耐環境特性を改善、材料の適用範囲を飛躍的に拡大
単層CNT融合新材料研究開発機構(TASC)と産業技術総合研究所は、ゴム材料に単層カーボンナノチューブ(CNT)を加えることで、世界最高水準の耐熱性、耐熱水性、耐酸・耐アルカリ性などの耐環境特性を持つゴム材料を開発しました。
2015年
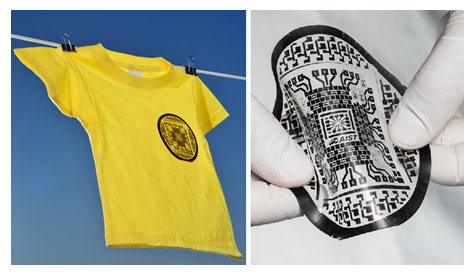
衣類のように柔らかく、丈夫なトランジスタを開発
-ハイヒールで踏んでも洗濯しても壊れない-
単層CNT融合新材料研究開発機構(TASC)と産業技術総合研究所は、スーパーエンジニアリングプラスチックの一種であるポリエーテルエーテルケトン(PEEK)にスーパーグロース法で作製した単層カーボンナノチューブ(SGCNT)を加えることで、世界最高水準の耐熱性と機械強度を同時に達成し、かつ射出成形可能な新しいスーパーエンジニアリングプラスチック「PEEK/SGCNT複合材料」を開発しました。
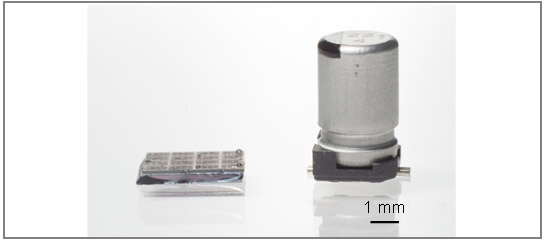
CNT集積化マイクロキャパシターを開発
アルミ電解コンデンサーと同等の性能で体積を1/1000に
スーパーグロース法による高純度・高比表面積の単層カーボンナノチューブ(CNT)を電極材料に、リソグラフィー技術を用いて、マイクロキャパシターの集積化を初めて達成しました。
2014年
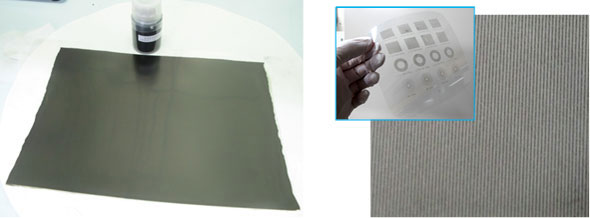
塗工・印刷可能な単層CNTコート剤を開発
単層CNTを低コストで利用可能に
単層CNT融合新材料研究開発機構(TASC)と産業技術総合研究所は、カーボンナノチューブ(CNT)を溶媒中に高濃度で分散させることによって、基板上に塗工・印刷が可能な単層CNTコート剤を得ることに成功し、一定の厚さを保った上で単層CNTを大面積厚膜塗工する技術 や単層CNTの微細パターンの成形を低コストで印刷する技術を開発しました。
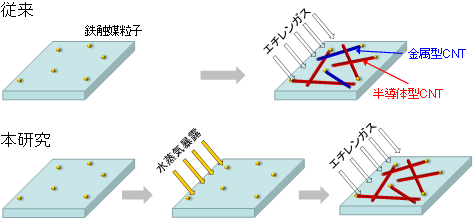
半導体型単層CNTを選択的に合成する技術開発に成功
最大98%の高い選択率を実現
金属触媒の状態をあらかじめ調整する合成手法を考案し、半導体型の選択率が高くなるほどカーボンナノチューブ(CNT)薄膜トランジスタの特性を向上させることに成功しました。
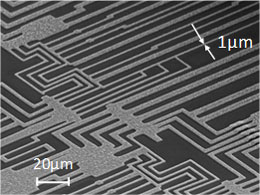
単層CNTと銅の複合材料で微細配線加工に成功
高電流に耐える高機能小型電子デバイスの配線が可能に
単層CNT融合新材料研究開発機構(TASC)と産業技術総合研究所は、単層カーボンナノチューブ(CNT)と銅の複合材料を用いて、銅の100倍の電流を流すことが可能な微細配線を基板上に作製する技術を開発しました。
2013年
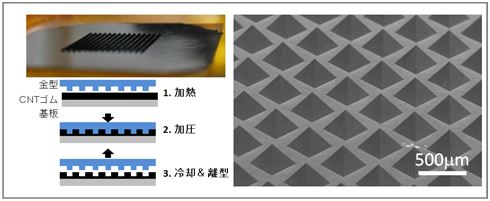
ゴムをナノメートルレベルの精度で金型成形
CNTを添加することで自在な表面加工が可能に
ネットワーク構造のカーボンナノチューブ(CNT)を添加することでゴムの柔軟性と加工性を両立しました。濡れ性、密着性、光学特性を制御した高機能ゴム開発への応用が期待されます。

銅の100倍まで電流を流せるCNT銅複合材料
今後のデバイス小型化・高性能化に対応できる配線材料のブレークスルー
単層カーボンナノチューブ(CNT)と銅を用いて、銅と同程度の電気伝導度をもちながら、これまでにない電流容量の複合材料を開発しました。227℃での電気伝導度は銅の約2倍であり、温度上昇による電気伝導度の低下が抑えられています。
2011年
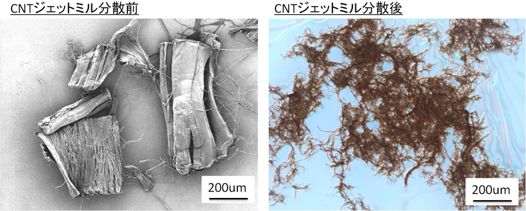
極少量の単層CNTを添加して作った導電性樹脂
帯電防止や静電気除去など多様な応用に期待
単層カーボンナノチューブ(CNT)を樹脂中に分散させる新しい手法を開発し、母材としてゴムを用いた場合、わずか0.01wt%の添加量で10-3S/cmの体積導電率を達成しました。
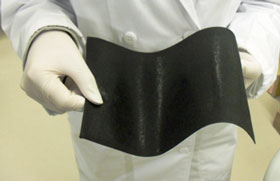
チタン並みの熱伝導率をもつ単層CNT/CF/ゴム複合材料
軽く、薄く、柔らかい放熱材料の実現に道
高純度の単層カーボンナノチューブ(CNT)とピッチ系の炭素繊維(CF)をゴム中に分散させることにより、金属チタンに匹敵する25W/mK の熱伝導率をもつ単層CNT/CF/ゴム複合材料を開発しました。
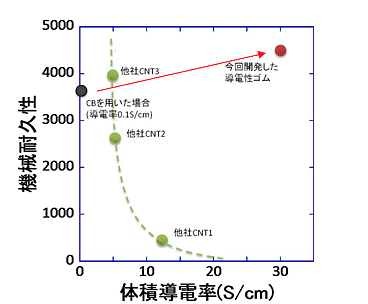
単層CNTを用いた導電性ゴムを開発
高伝導率、高機械耐久性を実現、フレキシブルデバイスへ道
低炭素社会を実現する革新的カーボンナノチューブ(CNT)複合材料開発プロジェクトの一環として、技術研究組合単層CNT融合新材料研究開発機構は、高伝導率・高機械耐久性を併せ持つゴム材料の開発に成功しました。スーパーグロース法で作製したCNT(SGCNT)を用いることで、従来のカーボンブラック含有導電性ゴムの100倍の導電率を有しつつ、約5000回の破断耐久試験に耐えうる材料を実現しました。
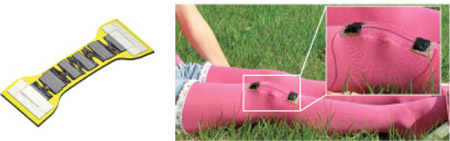
人体の動きを測定できるCNTひずみセンサー
金属製ひずみセンサーの50倍のひずみを検出可能
配向した単層カーボンナノチューブ(CNT)の薄膜を伸縮性のある高分子基板の上に貼り付け、CNT膜の電気抵抗変化によってひずみを検出できるひずみセンサーを開発しました。
大量生産で単層CNTの研究開発を加速
今後のデバイス小型化・高性能化に対応できる配線材料のブレークスルー
ナノチューブ応用研究センターは日本ゼオン(株)の協力を得て、スーパーグロース法による高純度単層カーボンナノチューブ(CNT)の大量生産設備の開発を進め、一日あたり600gの生産能力を実現しました。従来の実験室レベルの合成装置はバッチ式で、生産量は一日あたり1g程度に止まっていましたが、飛躍的に生産能力を向上させることに成功しました。
2010年

-196 ℃から1000 ℃までゴムのような粘弾性を持つCNT
軽さと丈夫さを兼ね備えた、広い温度範囲で利用できる粘弾性材料
ランダムなネットワーク状の構造を持つ高純度のカーボンナノチューブ(CNT)の構造体をスーパーグロース法を応用して作成しました。このCNT構造体は-196 ℃から1000 ℃までゴムのような粘弾性を示します。
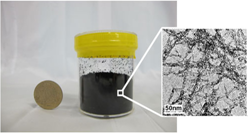
単層CNTで比表面積の大きな材料を開発
高エネルギー密度・高パワー密度の高性能キャパシタを実現
スーパーグロース法で合成した単層カーボンナノチューブ(CNT)の配向構造体を用いて、酸化によってCNTの先端や壁面に穴をあける「開口処理」を施すことにより、比表面積2240m2/gの繊維状材料を実現しました。
2008年
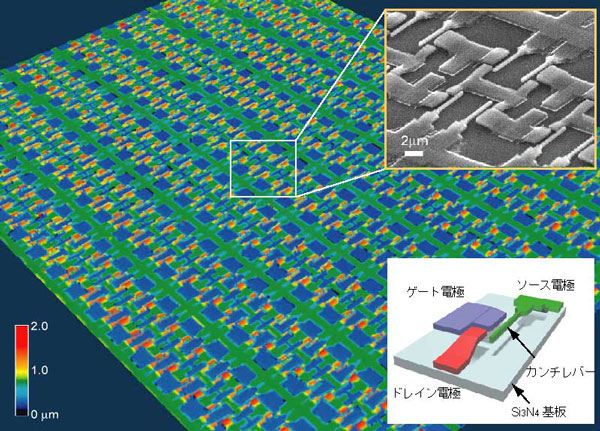
自由自在に設計したCNT3次元デバイスを実現
CNTデバイスの実用化に大きく近づく
カーボンナノチューブ(CNT)の高密度配向集合体“CNTウエハー”の開発により、設計したCNTデバイスを大量作製することに成功しました。
2007年
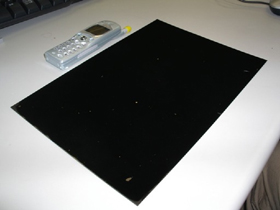
単層CNTの安価な大量合成法を開発
高純度の単層CNTの量産に弾み
ナノカーボン研究センターと日本ゼオン(株)は、共同で単層カーボンナノチューブ(CNT)の合成手法の一つであるスーパーグロース法を用いて、初めて大面積金属板上に直接大量の単層CNTを合成する技術を開発しました。
2006年
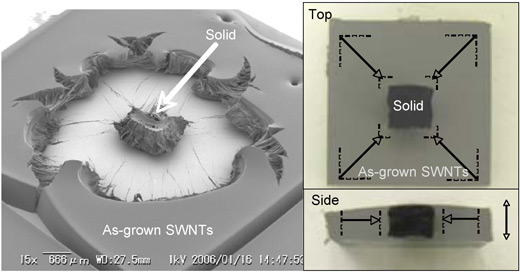
形状デザイン可能なCNT高密度固体
次世代のキャパシター開発へ弾み
単層カーボンナノチューブ(CNT)の優れた物理・化学特性を保持したまま、配向・高密度化した固体の開発に成功しました。
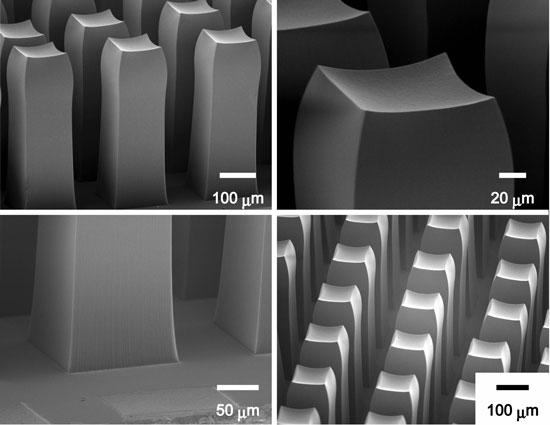
ディスプレイに応用可能なCNTを開発
二層CNTを高純度で合成
単層カーボンナノチューブ(CNT)の合成法の一つであるスーパーグロース法を改良し、二層CNTを高含有率で合成する技術を開発しました。二層CNTは、基板上から垂直に起立した形で成長し、2.2mmの高さの構造体を形成します。この構造体は世界最高レベルの85%以上の二層CNT含有率を実現しました。
2004年
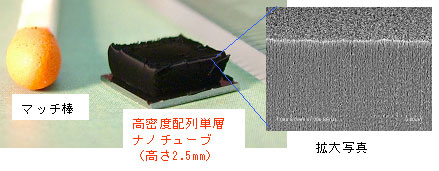
ナノカーボン研究センターは、単層カーボンナノチューブ(CNT)の合成手法の一つであるCVD法で、水分が触媒活性の発現・持続を促進することを発見し、CVD法における触媒の活性時間及び活性度を大幅に改善し、従来の500倍の長さに達する超高効率成長と従来の2000倍の超高純度の合成技術の開発に成功し、本手法をスーパーグロース技術と命名しました。