
西岡さんは、装置開発にあたって液体ではなく固体触媒を利用されましたが。
液体の中に触媒を拡散しておく方法では、溶液中から生成物を分離・回収する操作が必要です。分離プロセスにおける生成物のロスをなくす方法、また、触媒が反応系から出て行かない方法、すなわち触媒を反応系内に固定する方法が望ましいのです。化学プロセスを効率化するためには、固体触媒が適当なのです。ところが、私がこの研究を始めたときには、固体触媒を均一に加熱する方法が無かったのです。
電子レンジのような装置ですと、装置内のマイクロ波の乱反射や散乱をコントロールすることが難しいのです。マイクロ波が重なり合う部分は加熱エネルギーが強くなりますし、場所によっては全くあたらない部分もできてしまいます。そこで私は、定在波 を使って加熱する方法を利用しました。化学反応を行う反応器内に、定在波だけが存在する環境をつくれば、設計した通りの熱エネルギーを反応場に均一に提供できます。マイクロ波加熱に関わる研究分野が、確立された体系になっていない理由のひとつは、実験に再現性がないためなのです。従来のマイクロ波加熱に関する実験では、マイクロ波を照射したとき、試料を均一に加熱することが難しかったのですが、私達が開発した定在波を利用した加熱法は、少なくともその場所にどれだけのエネルギーがかかっているのかに関しては、設計に裏づけされた結果が出てきますので、再現性が高いのです。この結果は、学術的な意味も大きいですし、また産業界に与えるインパクトも大きいと考えています。
確かに、設計通りの結果が出て初めてコスト計算ができます。ところで、今回開発された装置を使ってどのような研究をされていますか?
例えば、VOC(揮発性有機化合物)の分解などを試みています。マイクロ波加熱を利用する分解法は、他の方法に比べて、対象となる化合物の幅広い濃度に対応できるという長所があります。酸化反応に優れた触媒を利用して有機物を酸化分解する方法により、様々な種類のVOCを分解できると考えています。
この場合、マイクロ波加熱による殺菌効果も併用できます。他にも、パラジウム薄膜 を利用した水素分離装置の開発も行っています。今後は、マイクロ波を利用した有機合成反応にもチャレンジしようと考えています。 |
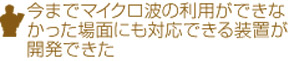
この装置は、どのような方を対象にしたものですか?
これは経済産業省の受託費の中小企業支援型という枠組みで研究させていただいているものです。今回の私のプロジェクトの目的は、研究室で使ってもらう実験装置をつくる事なのです。研究者の方がよく行われている実験系で、マイクロ波をかけてみたらどうなるのか、今まで装置の制約からマイクロ波の利用ができなかった場面にも対応できる装置になると期待しています。
私の装置で特徴的なのは、発振器にマグネトロンではなく固体素子を利用している点です。固体素子は半導体の一種なので、容易に発振する周波数を制御することが出来ます。具体的には、周波数2.3〜2.7GHzの範囲なら、この装置ひとつでデータをとることが出来ます。反応器の中に入れる試料が変更されたときなど、従来なら反応器そのものの寸法を変更しなければならなかった場合でも、発振周波数を変えるだけで対応できるようになります。
また、マイクロ波を利用する反応系は、従来はバッチ式が主流でしたが、今回開発した装置は、フロー式ですので、産業化などを目指した研究にも応用できると思います。また、フロー式の利点として、装置の末端にガスクロマトグラフィーなどの分析機器を接続すれば、実験結果がリアルタイムで確認できるという面もあります。東北センターの中に、この装置を使える環境があり、効果が出るかどうかをまず試せますので、ご興味のある方は是非、ご連絡ください。
非常に魅力的な装置ですね。本日はどうもありがとうございました。
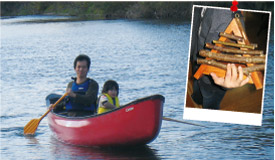
西岡さんお気に入りの写真:お子さんと一緒にカヌーを漕ぐ西岡さんと、子供達と作ったバードハウス。
毎日、楽しく過ごすことを心がけている西岡さんは、週末はご家族でキャンプをするなど、アウトドアを楽しまれているそうです。
|