
RESEARCH
Research List
Development for an advanced powder metallurgy technique
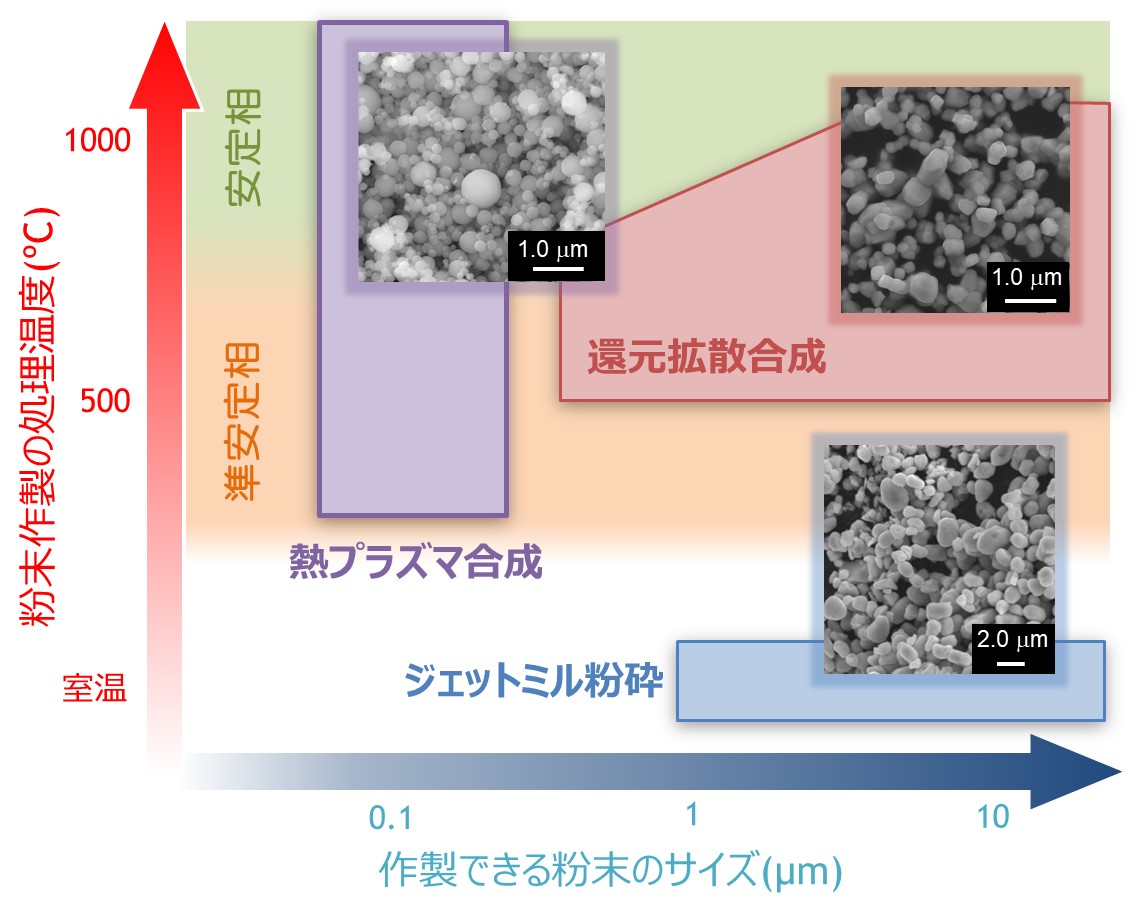
For exceeding performance of present neodymium magnets, existing techniques are not sufficient. To make its magnets further high coercivity ever before, it is needed a raw material powder which has ultra-fine and round shape, which normally unable to get via a pulverization approach. Besides, in order to break a limited wall of existing saturated magnetization, non-neodymium magnetic compounds, a hard synthetic material, would be required to gain in single-crystal powder. Since non-neodymium magnets are poor-sinterable and promptly degrade due to oxidation, it is necessary to be sintered with high density without oxidation. Thus, a key for producing post-neodymium magnets is “discovery new powder metallurgy technology”.
- Developing chemical powder synthesis technique(reduction diffusion method)to produce synthesis high quality sub-micron rare earth magnetic powders.
- Developing physical powder synthesis technique which allow to synthesize rare earth magnetic nano-powders.
- Developing a process of low-oxide powder synthesis technique, fine grindingーcompactionーsintering, under atmosphere in its oxygen concentration less than0.5ppm, and coating techniques to cover with various materials on surfaces of metal powders without any oxide phases.
- Aiming advanced microstructure control, such as crystal orientation control, our team develops a powder consolidation technique utilizing shear force and large deformation such as a powder rolling.
Creating new stronger magnets exceeding neodymium magnets
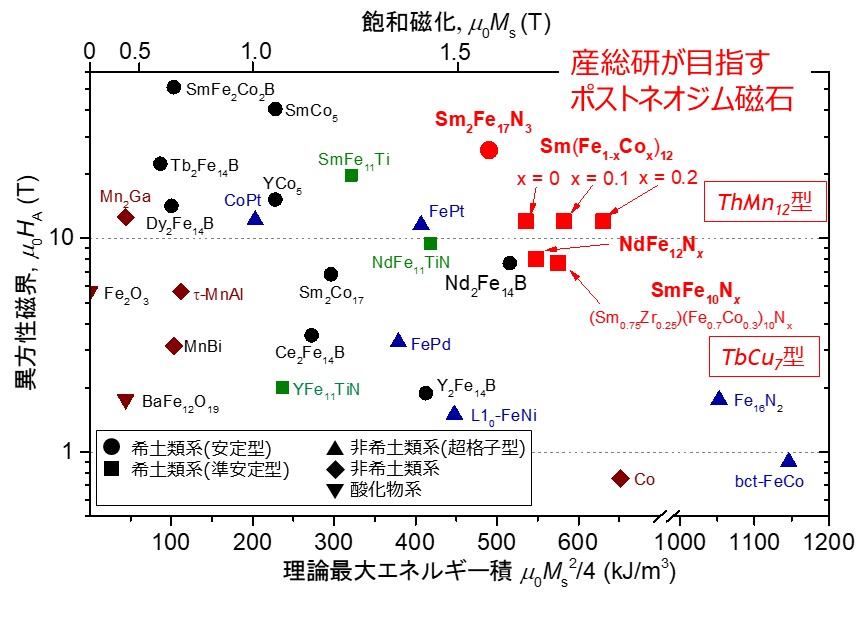
-Samarium iron nitride-Sm2Fe17N3 is the most prospective new materials for post-neodymium magnets because it can be expected to have three times as high coercivity as neodymium one. On the contrary, nobody can achieve the fact in truth. Furthermore, Sm2Fe17N3 has been thought that it would be difficult to sinter due to a degradation caused by heating. “metastable rare earth magnets” and “nanocomposite magnets” are also expected to their massively stronger magnetic performances compared to existing materials, however they have not been realized yet. In our group, we set a goal to realizing next-generation magnets via developing and utilizing our unique powder metallurgy techniques.
- Our group have realized to produce Sm2Fe17N3 powders which have huge coercivity of 2.8 T or more by submicron-sized powder sintering technique via chemical powder synthesis technique
- Developing physical powder synthesis technique which allow to synthesize rare earth magnetic nano-powders.
- Our group have showed a feasibility of the world's first anisotropic Sm2Fe17N3 sintered magnets by a development of low-oxygen process which have based on our revealed mechanism of the thermal degradation during sintering.
- Our group aim to realize to create metastable rare earth magnets and nanocomposite magnets known as a type ThMn12 or a type TbCu7 utilizing thermal plasma method and sever plastic deformation approach.
A synthesis technique for
creating high quality submicron rare-earth magnetic powders
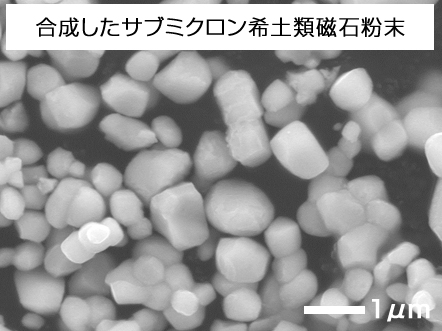
In a field of magnetic powders, particle size places one of significant parameters. In particular, making particle size into submicron size is a promising approach to produce high coercivity magnetic powder. We research on a reduction-diffusion technique, and high quality submicron-size rare-earth magnetic powders shown in figure have been prepared without pulverization process.
Development of thermal plasma synthesis for metal nanopowder
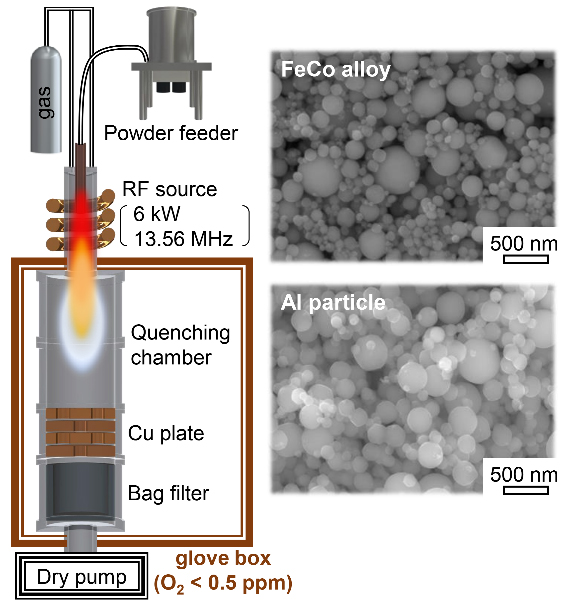
We developed a new process to prepare nano-sized metal powder especially for easy oxidizable metals and aims in applying the process to prepare permanent magnetic materials and metal matrix composites materials. In order to prepare nano-sized powders, we focus on an induction thermal plasma (ITP) technique as a bottom-up process*. This process can be realized to prepare fine metal powder even when the metals has high melting point or high ductility. However, it is difficult to handle the nano-sized metal powders in the atmosphere since metal nano powders are highly reactive with oxygen and moisture. Therefore, we have constructed a new glove box system to collect powders and evaluate under low oxygen atmosphere (see schematic illustration of experimental set up). Using this new system, we have succeeded in synthesizing almost "bare" Al powders and FeCo metal powders (see SEM images).
*The induction thermal plasma (ITP) is produced by high frequency electromagnetic induction, and its temperature reaches as much as 10 000 K. When a raw powder material is injected into such a high temperature plasma, the powder is vaporized and fine particles are produced though a process of nucleation, condensation and coagulation with a high cooling rate of 103-106 K/s.
Development of low-oxygen powder metallurgy technique
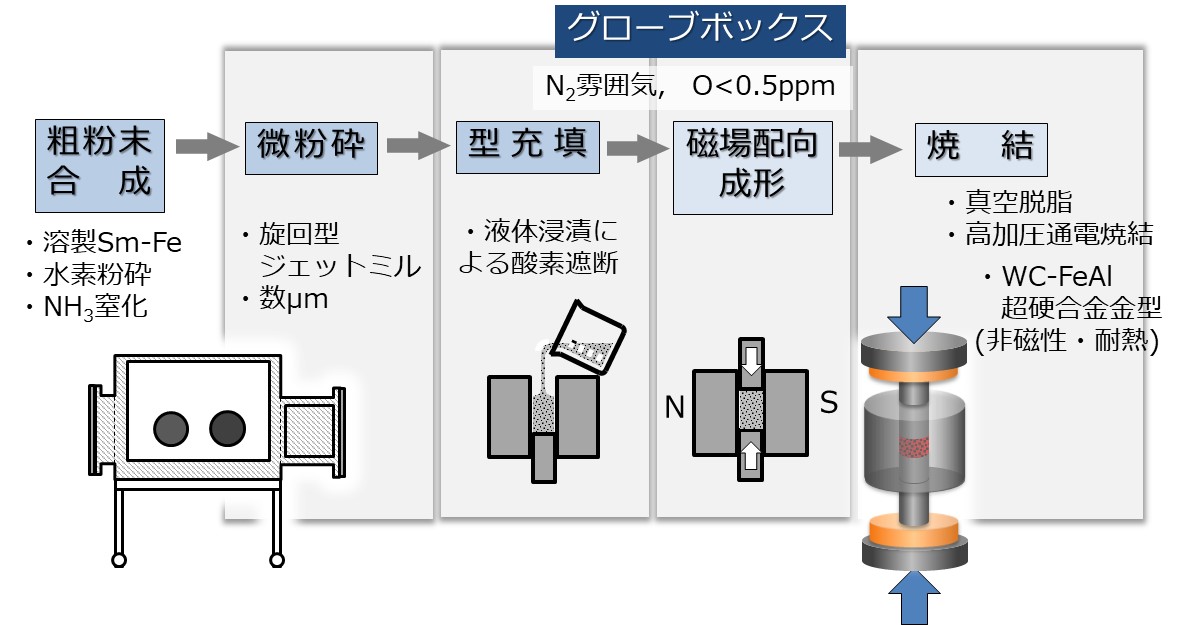
In metallic materials produced via powder metallurgy technique, an oxide film on powder surfaces greatly influences on its density and its properties on finished products. In particular, an oxide film of permanent magnetic materials caused decreases in coercivity and remnant magnetization. A Sm2Fe17N3 magnet which is studied in our group also shows that its coercivity drastically declines during sintering because of surface oxide film. Our group, therefore, has constructed a system that enables us to conduct whole powder metallurgy processes starting from grinding powers to sintering under atmosphere with low oxygen concentration below 0.5ppm.
Development of low-oxygen pulverization technique
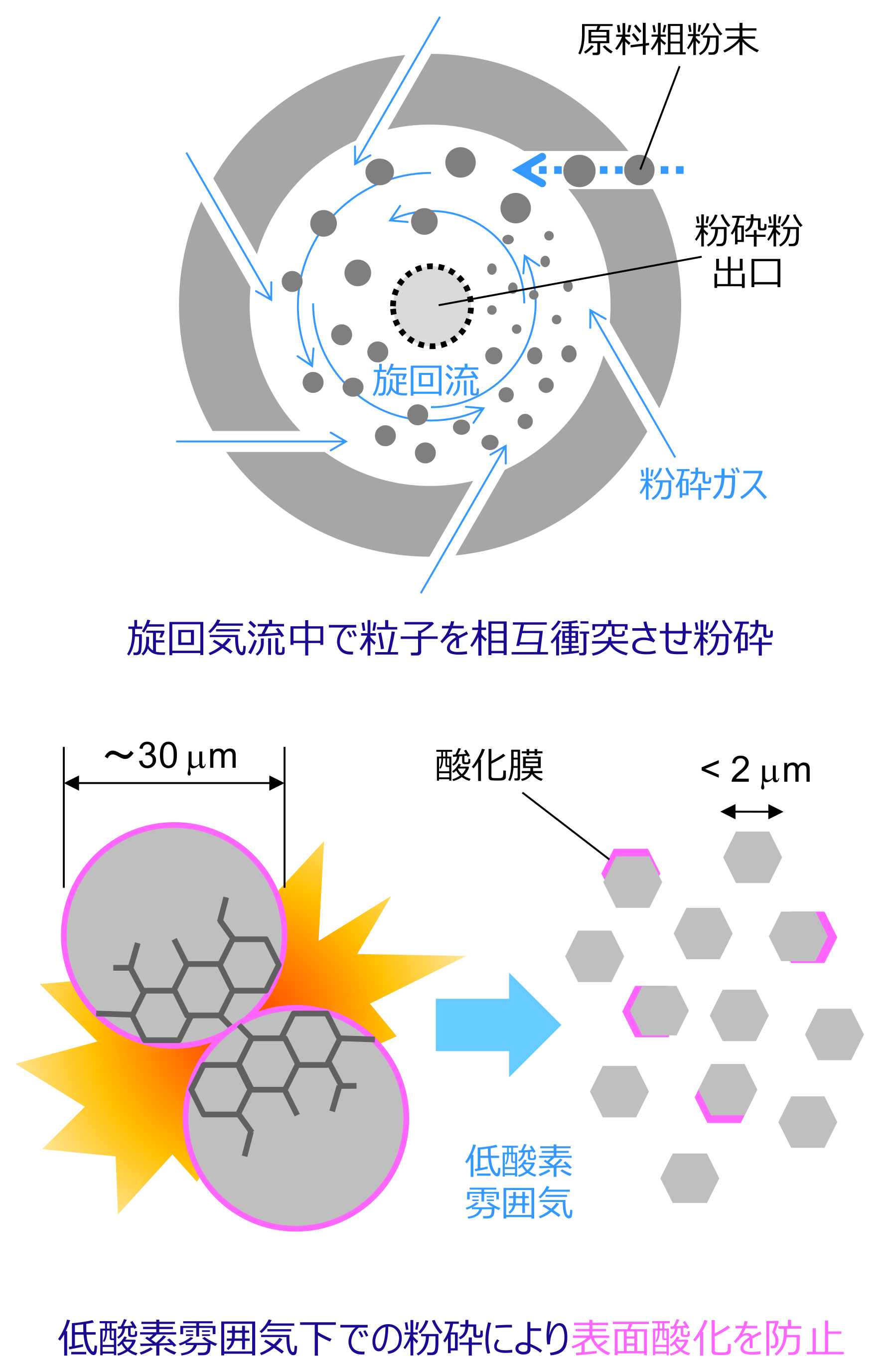
Many of prospective new materials for post-neodymium magnet easily get to performance degradation because of oxidation. To produce sintered magnets, therefore, it is highly needed to conduct the whole process under low-oxygen circumstances. In particular, at the most upstream pulverization step, producing how high-performance and low oxygen content powders is the most significant key to determine a baseline performance of the whole low-oxygen process.
Hard magnetic materials team develops pulverizing technology for grinding coarse powder into fine one utilizing spiral flow type jet mill under atmosphere with oxygen concentration of 0.5 ppm or less. Newly formed surface via fine grinding is kept non-oxidized for a long period, which causes that the ratio of the oxidized portion to the total surface decreases in inverse proportion to the specific surface area. Our team has succeeded in producing low-oxygen fine powders with 1~2μm particle diameter from 20~30μm coarse powders, by optimizing the kinds and pressure of grinding gas and times of repetitive grinding process.
Development of powder coating technique
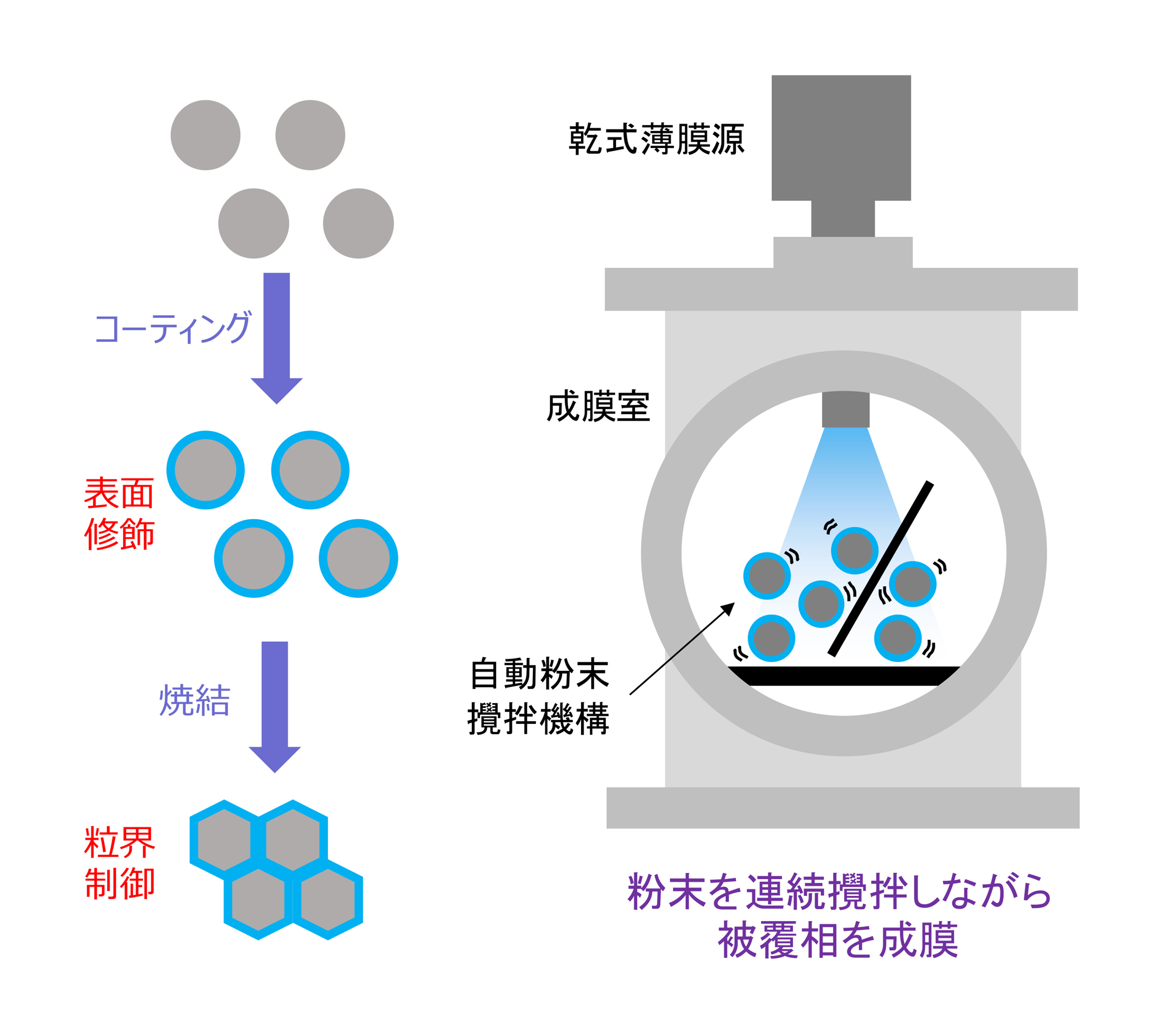
It is well known that crystal grain boundary properties greatly influence performances of permanent magnets. “Grain boundary control“ is therefore an important keyword in research of magnets. In materials produced via powder metallurgical processes, "surfaces" are made into grain boundaries through the sintering, which indicates that issues of the grain boundary control can be replaced by ones of powder surface modification.
From this point of view, the hard magnetic materials team develops a technique to coat the surface of a powder with a nanoscale film of various kinds of materials. Powders are coated with covering materials by a dry thin film technique during continuous powder agitation in a vacuum chamber. Since this method can be used for a variety of materials due to its high versatility, we can tune grain boundary properties, adjusting chemical composition, film thickness, and combination of the materials. Additionally, we integrate this technique into the low-oxygen powder metallurgy process, and make it possible to coat metallic surfaces of powders with covering materials without inserting oxide phases.
Development of severe plastic forming processes
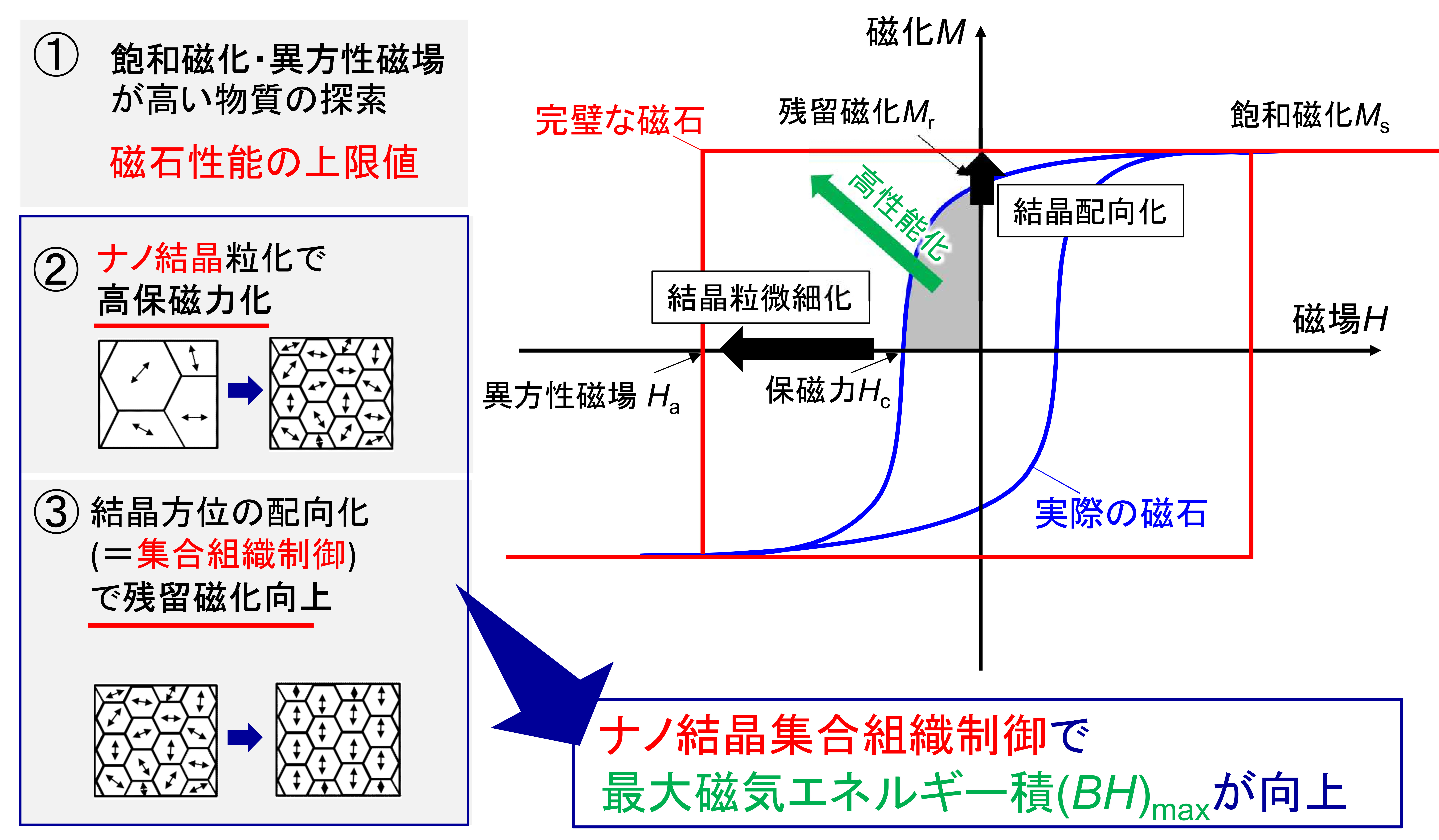
Severe plastic deformation (also known as forging, working, etc.) is a method to produce a piece having an arbitrary shape by mechanically hammering, pulling or stretching materials. Press working and rolling of metallic sheets are very typical examples. This kind of methods have another secret advantage that microstructure inside materials can be controlled, making it possible to control the size of crystalline grains as well as alignment of crystallographic orientations of individual grains (=referred to as texture) inside materials. In the field of permanent magnets, grain refinement and texturing are highly important for achieving high performance magnets as shown in the figure. In our group, we have been working on optimizing the micro/nanostructure of nanocomposite magnets, which is one of the most prospective permanent magnet materials, by using various severe plastic deformation methods such as high-pressure torsion and hot die-upset. In parallel with this, development of a new processing route based on powder rolling method to produce a bulk Sm-Fe-N magnets (a great magnet material but extremely challenging to consolidate by conventional sintering!) is under progress.
Synthesis of Sm2Fe17N3 magnetic powder
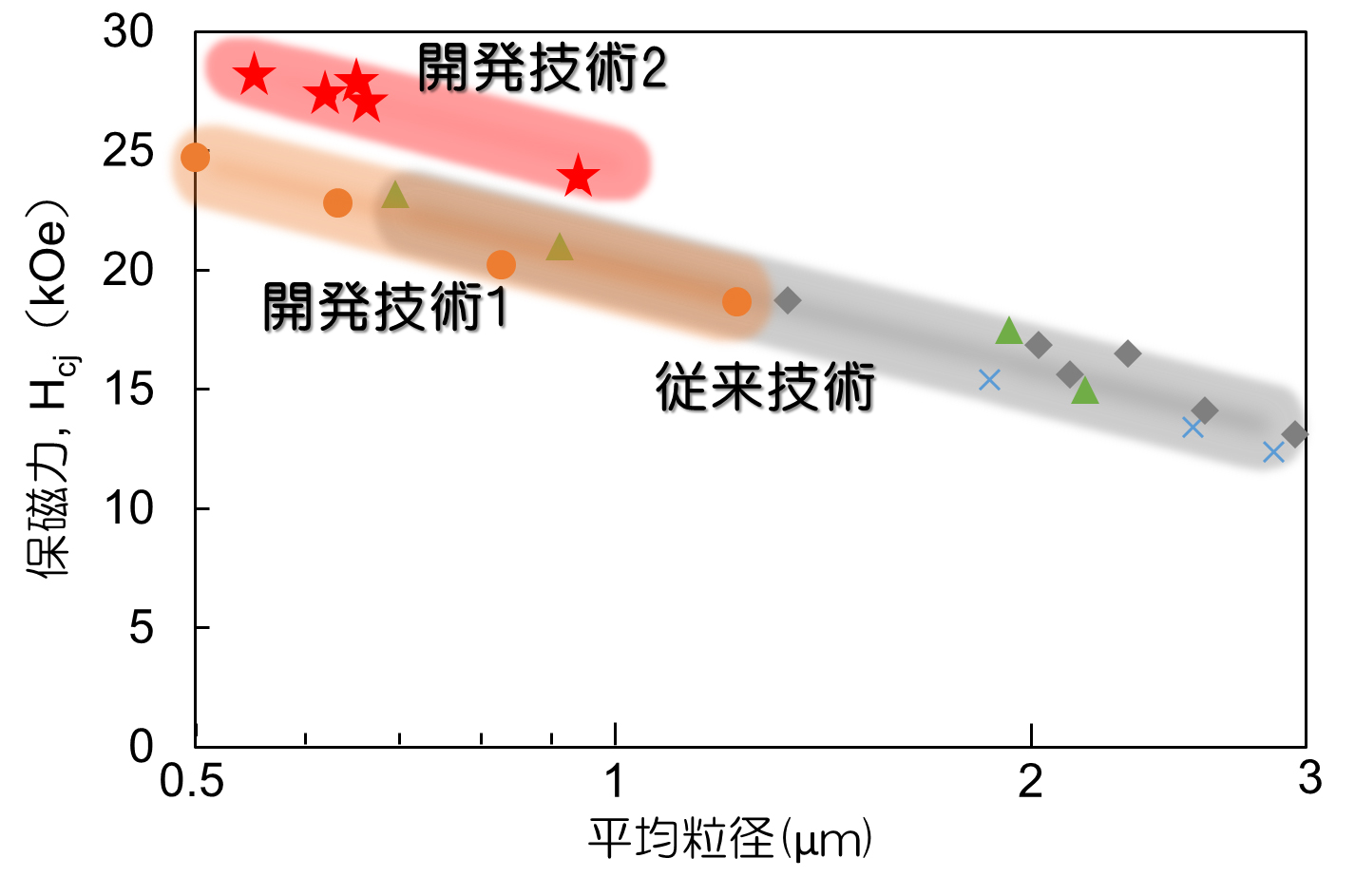
Coercivity is known to be increasing as particle size being smaller. However, there was no reports for preparation of a submicron-size powder with high coercivity which was expected from the particle size. Our group revealed hydrogen, which was generated in water washing process, was intercalated in Sm2Fe17N3 crystal structure and it decreased coercivity. De-hydrogenation treatment removed the hydrogen, and it was revealed that coercivity gets stronger even in submicron size. Recently, by further developments for reduction-diffusion process, our group are making a success for synthesis of a Sm2Fe17N3 magnetic powder which has high coercivity ever before.
Toward a world’s first Sm2Fe17N3 sintered magnet
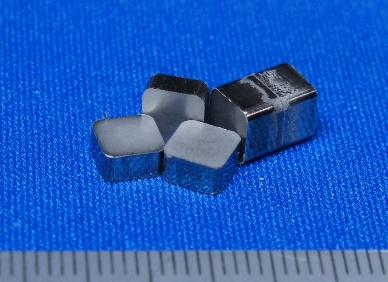
A Sm2Fe17N3 magnet has superior performance to a neodymium magnet under circumstances in high temperature inside a motor. However, since it had been a problem that its coercivity becomes massively declined during its sintering, creating a Sm2Fe17N3 magnet had never been achieved. On the contrary, in 2012 researchers, Takagi et al., discovered that an oxide-film on the powder surface caused decreasing coercivity, furthermore, in 2015 they revealed experimentally that it is possible to create higher coercive Sm2Fe17N3 sintered magnets unless the powder can be sintered without oxidation.
Currently, aiming better magnetic performance of sintered magnets, our group is developing grain boundary control and also try to realize to create superior sintered magnets to neodymium ones
Metastable type magnets
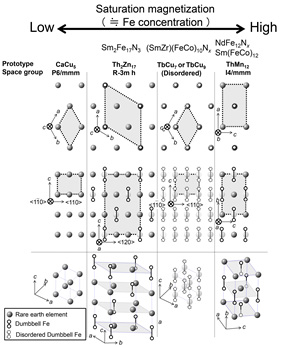
The induction thermal plasma (ITP) is produced by high frequency electromagnetic induction, and its temperature reaches as much as 10 000 K. When a raw powder material is injected into such a high temperature plasma, the powder is vaporized and fine particles are produced though a process of nucleation, condensation and coagulation with a high cooling rate of 103-106 K/s. Using this quenching process, we work on preparation of fine powders such as (SmZr)(FeCo)10Nx with TbCu7 structure, NdFe12Nx and Sm(FeCo)12 with ThMn12 structure. Furthermore, we also develop nano composite magnets based on those powders.
Challenge to create nanocomposite magnets
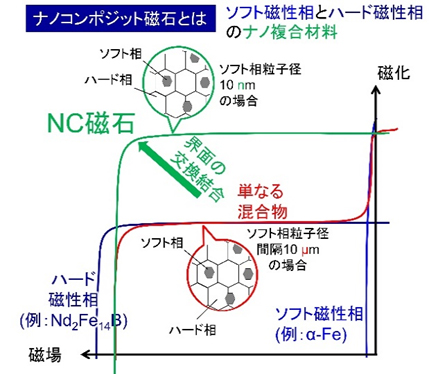
A nanocomposite magnet (also known as an exchange spring magnet) is one of the promising new generation permanent magnets. This class of materials possesses a nano-sized composite microstructure that consists of a hard magnetic phase with high coercivity (e.g. Nd2Fe14B) and a soft magnetic phase with high magnetization (e.g. pure iron) as shown in the figure. A prediction by a classical theory claimed that an innovative magnet which is twice as strong as Nd2Fe14B magnets can be obtained because of exchange interaction at soft/hard interphase boundaries, but the actual figure of merits reported by many experimental works to date are disappointingly lower than the value expected from the theory. The reason was attributed to difficulty of texturing for a long time, but recent research works that combined first principle calculations and thin film experiments indicated the necessity to control the orientation relationships of soft/hard interphase boundaries on top of texture. In our group, we are aiming at producing anisotropic bulk nanocomposite magnets through development of a brand-new processing method utilizing severe plastic deformation.