Digital Manufacturing
About
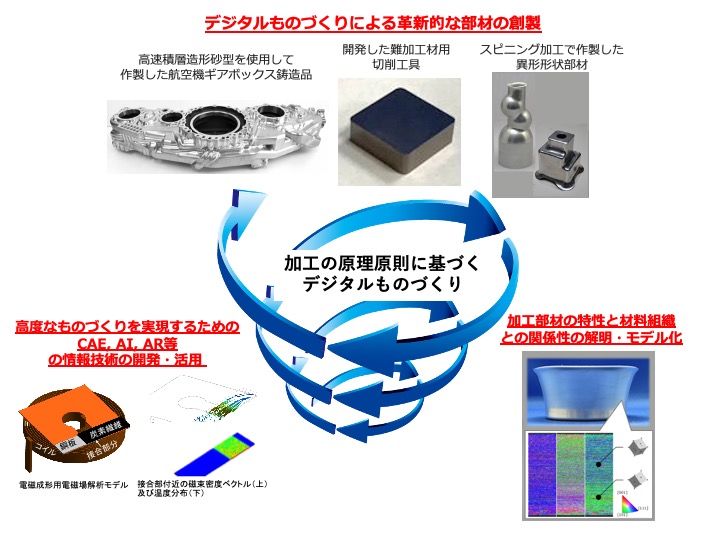
CAE and other information systems are being introduced at design and manufacturing processes. Digital manufacturing is a technology that, in addition to these information systems, links the latest AI, robot control technology, etc., which have not been applied until now, with processing technologies such as plastic forming, casting, welding and additive manufacturing to realize more efficient processing and advanced processing. The division is also working on clarifying the relationship between the properties of processed materials and microstructure, and modelling processing phenomena by experimental observation. We are working on contributing to the realization of DX in manufacturing technology by promoting digital manufacturing based on the principles of processing phenomena.
points
- 1 Realizing efficient manufacturing and advanced manufacturing by elucidating the relationship between material properties and by modeling manufacturing phenomena.
- 2Realization of innovative manufacturing processes through more advanced linkages between information systems such as CAE, AI, robot control technology, modelling technology of manufacturing phenomena, etc. and manufacturing technology.
Feature
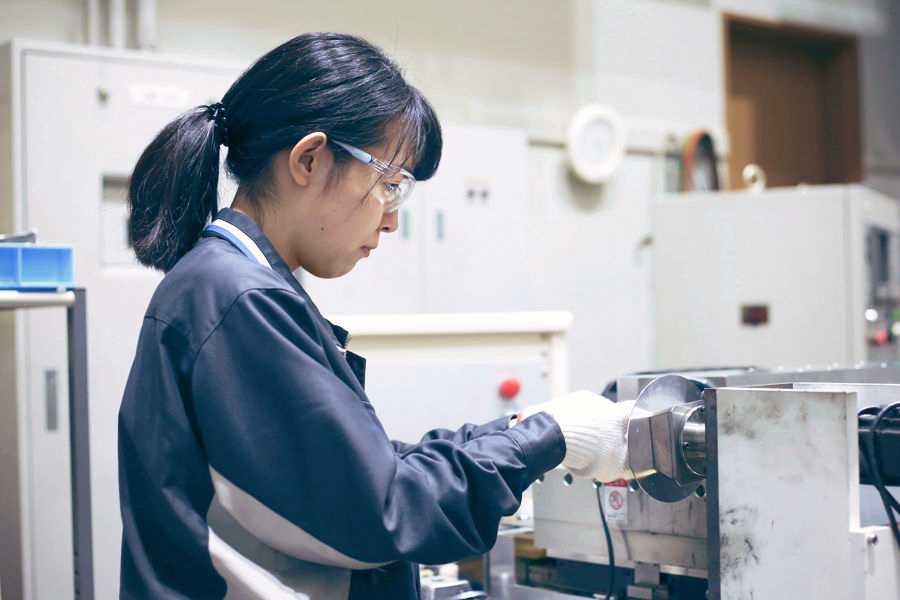
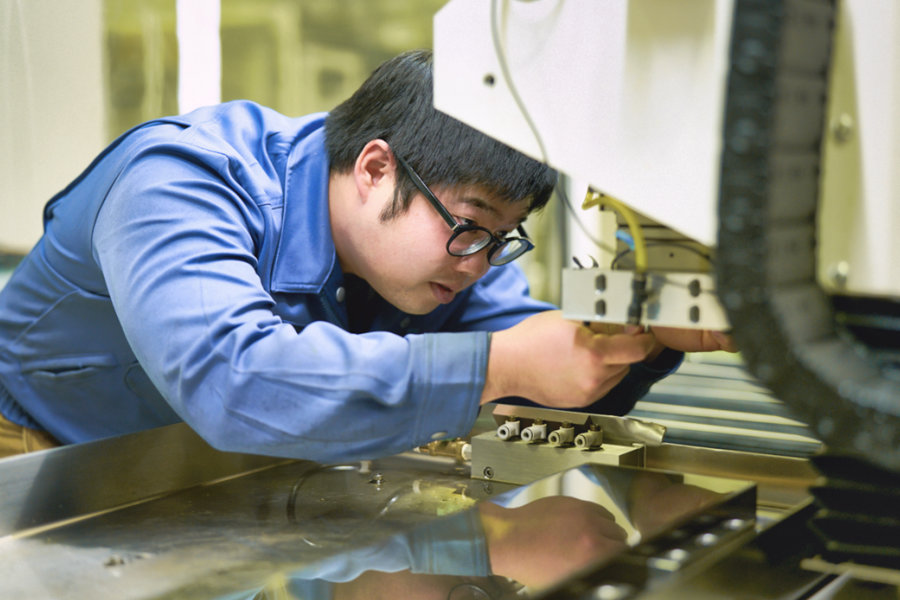
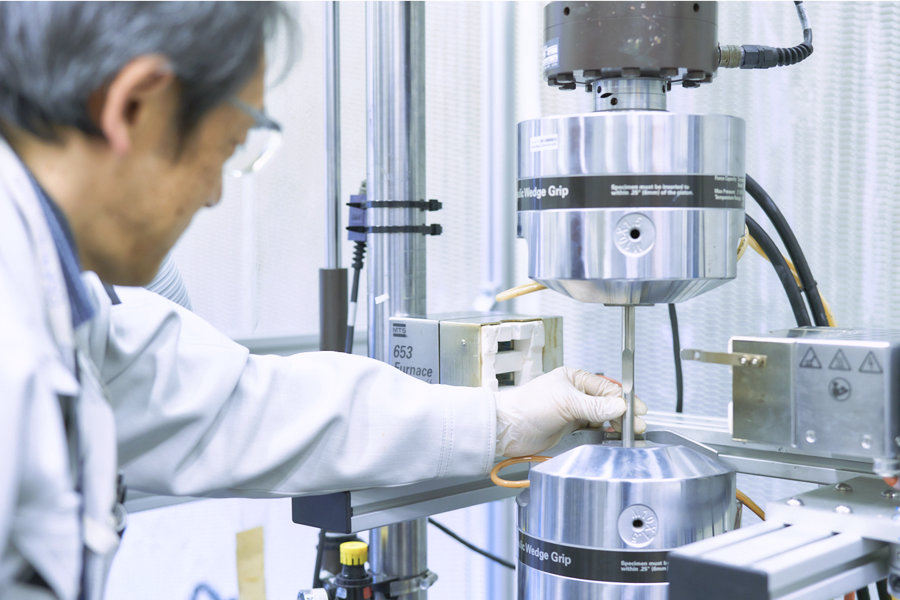
In recent years, initiatives related to DX, such as IoT and connected factories, have been actively pursued in order to maintain and improve Japan's industrial competitiveness. However, in order to realize DX in manufacturing and material processing, connecting technologies such as IoT alone are not sufficient. In addition to its technologies, It is essential to develop modelling and collect data on material properties and material processing with the development of technologies for their use. By taking advantage of the fact that our department has a large number of researchers who are familiar with each material processing, we are elucidating the relationship between the microstructure and the properties of materials processed by plastic forming, casting, welding, additive manufacturing and other processes. We are also studying the latest AI technology, the upgrading of materials processing technologies through the elucidation and modelling of the elementary processes of materials processing phenomena, the creation of materials processing databases built with a focus on worker's intuition, and the manufacturing simulation technologies for each materials processing, materials property evaluation, and materials reliability evaluation and so on. In addition to advancing these technologies, we are also working on the development of innovative materials processing technologies through collaboration and combination of these technologies.
Result
-
1.Development of spinning for non-circular shaped part by robotic control technology
We developed spinning for a non-circular shaped part that has an ellipse or polygon cross-section and an eccentric, inclined and curved axis. This technology results from the combination of 3D-CAD for product shape design, CAM for tool-path calculation and robotic control technology. The combination enables to calculate the tool-path using 3D-CAD data and leads to easily form a complex shaped part whose cross-section varies with the axis direction.
-
2.Development of an Interactive Process Design System for High-Pressure Die Casting
We have developed an interactive process design system for high-pressure die casting that combines CAD technology and highly efficient particle method simulation to enable runner geometry changes while performing analysis. Using the interactive design system, we conducted a high-pressure die casting process design of a heat sink for a power semiconductor. Using the interactive design system, we confirmed that the design of the high-pressure die-casting process can be made nearly three times more efficient than the conventional procedure.
-
3.Developments of cermets with excellent high-temperature hardness and oxidation resistance, suitable for cutting difficult-to-cut materials
Ti(C, N)-W cermets with nano-level ultrafine network structures have higher high-temperature hardness and oxidation resistance than conventional cemented carbide K10. Besides, the cermets show much smaller wear rates than the cemented carbide when cutting super-stainless steel and Inconel alloys at high cutting speeds.
-
4.Development of technology for suppressing shear droop by adding torsion
In the shearing process used when cutting wires and bars, we have developed a shearing process that adds twisting in order to suppress the droop that occurs during processing. We confirmed that by adding twist, the shearing force required for cutting can be reduced and the occurrence of droop can be suppressed. In shearing, strain is concentrated on the cut end surface, which causes droop. However, by adding torsion, we confirmed that the strain was uniformed throughout the material. As a result, we proved the mechanism of droop suppression from a material perspective.
-
5.Capturing the pouring action of a skilled worker using AR markers tracking technology, and development of molten metal flow simulation technology based on the captured motion.
As a technology to measure the pouring motion of workers, a ladle motion measurement technology using AR markers has been developed. By placing AR markers on the ladle and the mold and capturing them with a video camera, the movement of the ladle can be measured and recorded. In addition, a particle method thermohydraulic/solidification simulator that can input these measurement data has been developed. As a result, casting simulation can be performed based on the pouring motion as shown in the figure below. This developed technology makes it possible to analyze and evaluate the pouring motion of skilled workers and the flow of molten metal, which contributes to the improvement of the quality of castings.
-
6.Clarification and advancement of electromagnetic forming phenomena by electromagnetic field analysis and thermal conduction analysis
By incorporating electromagnetic field analysis and thermal conduction analysis using CAE into electromagnetic forming technology, which uses electromagnetic force to plastically deform metals, we have made further progress in elucidating the phenomena of the forming process. As a result, it is now possible to perform not only plastic forming but also joining of dissimilar materials, such as joining metal to metal or metal to carbon fiber-reinforced plastic.