Advanced Coating
Creation of highly functional films using photoreactive coating and hybrid coating technologies and construction of circular manufacturing
About
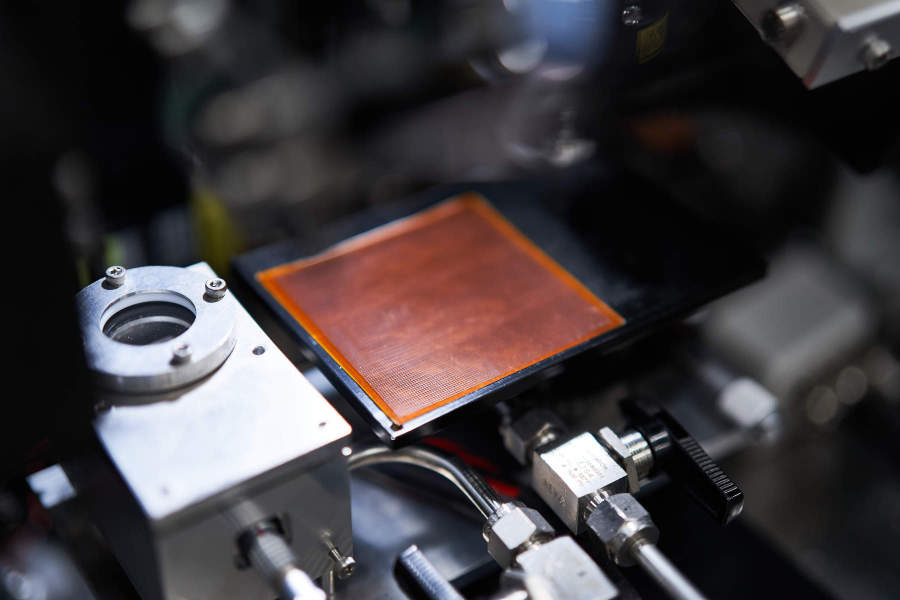
Our research institute is working on the development of new AIST original ceramic coating methods for the construction of circular manufacturing. The photo-assisted chemical solution deposition (PCSD) method is a method, which is a low-temperature deposition based on the chemical solution method that uses light to crystallize ceramic films. It is expected to be a new deposition method that is superior in making ceramic films flexible, reducing deposition energy, and saving resources. The hybrid aerosol deposition (HAD) method can form dense to porous films, and is expected to be a technology to add surface functions to materials with complex three-dimensional shapes. The division is committed to further deepening the HAD method and contributing to the realization of carbon neutrality and the enhancement of industrial competitiveness.
Points
- 1Development of ink, coating/film deposition, and photoreaction technologies that combine improved functionality and high durability
- 2On-demand repair and upgrade cycle process development for the establishment of circular manufacturing
- 3Creation of functional surfaces that enable response to environmental constraints such as carbon neutrality
Keywords
Photo-assisted chemical solution deposition (photometallolysis, nanoparticle photoreaction method, hybrid solution photoreaction method), multi-material, hybrid aerosol deposition (HAD)
Feature
Photoreactive coatings such as PCSD enable low-temperature deposition using light energy and, at the same time, uniform mixing of a wide variety of metals, making it possible to develop new materials at low temperatures and high speed. In particular, ceramic coating on plastic, which has been difficult in the past, realizes flexible and lightweight functional materials. In addition, high-functional and highly durable components are also possible by coating metal and resin components. Since reliability evaluation is essential for the practical use of such components, we are also conducting research on accelerated degradation tests, film formation, functional manifestation, and mechanism elucidation of degradation, etc.
Result
-
1.Photo-reactive coating (PCSD, photo-CVD, photo-sputtering, etc.)
PCSD is a method of coating ceramics, metals, and resin substrates with metal-organic compounds, nanoparticles, or mixed solutions (hybrid solutions) by various methods, and after drying, a metal oxide film is formed by a UV light reaction. A crystallized film can be produced simultaneously with coating by a multi-step photochemical reaction with different laser energies and repetition frequencies. It can also be applied to crystal growth processes in vapor phase film forming such as CVD and PVD. We have succeeded in processing the powder into a powder suitable for AM use, such as by imparting / high filling properties / low defects.
-
2.Polycrystalline and epitaxial films and their mechanism
Polycrystalline films and epitaxial films can be efficiently grown at low temperatures by using substrates with laser light absorption. Epitaxial films such as La1-xSrxMnO3, Pb(ZrTi)O3, SmBaMn2O6, SnO2, and VO2 thin films have been fabricated. The mechanisms of epitaxial growth of composite oxides on ceramic substrates and polycrystalline growth using photochemical reactions have been investigated in detail by quantitative analysis of photochemical and photothermal reactions to advance the process and to propose next-generation devices.
-
3.Flexible ceramic film
Traditionally, ceramic films have been made using base materials such as glass and ceramics because they are formed in a high-temperature process of 500°C or higher, but AIST has developed a new manufacturing process to fabricate various ceramic materials on resin by utilizing the extremely rapid reaction and wavelength selectivity of the photoreaction process. AIST has developed a new manufacturing process to fabricate various ceramic materials on resin by utilizing the pulse reaction and wavelength selectivity of photoreaction processes. This technology enables flexible resistor films, flexible thermistor films, high-brightness phosphor films, high-mobility transparent conductive films, and other materials to realize lighter components and higher functionality.
-
4.Development of a three-dimensionally driven plasma torch
Radio-frequency inductively coupled plasma (rf-ICP) is often used in the HAD method, but the equipment is large and it is difficult to operate it in three dimensions. We have improved the rf-ICP torch and succeeded in miniaturizing it to a level where it can be mounted on an industrial robot.
HAD coating deposition using a three-dimensionally driven rf-ICP torch. The plasma torch is mounted on an industrial robot to apply a ceramic coating to a 40 cm diameter aluminum ring.
-
5.Dense alumina coating by HAD method
The HAD method makes it possible to deposit dense, crack-free ceramic coatings. An alpha alumina coating with a Vickers hardness of 1800 HV, which is close to bulk hardness, is also obtained.
Figure Comparison of alumina coatings deposited by the HAD method and those deposited by the plasma spray method. There are no microcracks or pores, which are often observed in plasma sprayed coatings.
-
6.Sealing technology for porous structures by the HAD method
In the HAD method, the bonding force between particles is improved by plasma-assisted spraying. This plasma-assisted process makes it possible to deposit dense ceramic coatings on porous substrates.
Related Links
- Advanced Coatings Alliance
- https://adcal.org/