ポイント
- 一度の成形で狙い通りの製品寸法に成形できるAIへら絞り(スピニング)加工技術を開発
- 少ない学習データでローラーの最適な動作経路を瞬時に決定し、試作時間を大幅に短縮
- 加工条件の決定支援AIツールとして、素形材産業における小規模製造現場での活用を期待
概要
国立研究開発法人 産業技術総合研究所(以下、「産総研」)製造技術研究部門 素形材加工研究グループ 権藤 詩織 研究員、荒井 裕彦 テクニカルスタッフは、一枚の金属板から立体形状に成形するへら絞り(以下、「スピニング」)加工において、AIを使ってローラーの最適な動作経路(以下、「ローラーパス」)を瞬時に決定する技術を開発した。短時間で容易に、立体形状の高さや板厚が狙い通りの寸法となるように成形できる。
スピニング加工は、回転する金属板の一部にローラーを押し当てて少しずつ変形させ、立体形状に成形する加工法である。プレス加工などの他の塑性加工法とは異なり、最終形状のみの金型さえあれば成形できるという特徴から、短時間での製品試作や多品種変量生産の場面で利用価値が高い。しかしながら、製品の高さや板厚などの寸法はローラーの動かし方ひとつで大きく変わってしまうため、狙い通りの寸法となるように加工するには、ローラーパスの決定に試行錯誤を重ねる必要があり、多大な時間と労力が必要であった。今回開発した技術では、少数のデータを使い、ローラーパスと寸法の関係をニューラルネットワークでモデル化し、さらに、反復解法と呼ばれる計算技法を用いて、具体的な目標仕様を実現する最適なローラーパスを瞬時に決定できる。これにより、一度の成形で狙い通りの寸法となるような加工が可能となる。少数のデータをAIに学習させ、目標仕様から最適加工条件を逆算して求める手法は即応性が高く、様々な素形材加工手法へも適用が期待できる。
なお、本成果の詳細は、2022年1月12日にJournal of Intelligent Manufacturingでオンライン公開された。
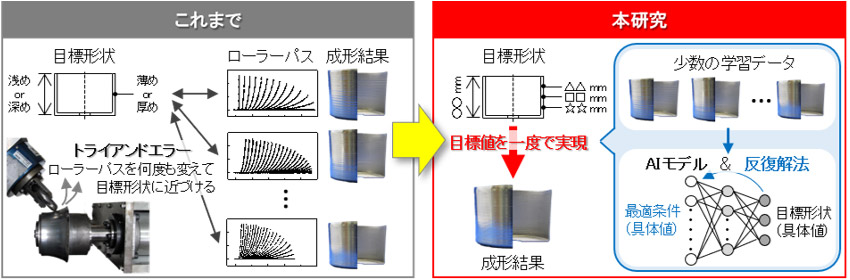
少数の学習データによるAIを使った最適なローラー動作経路(ローラーパス)の決定
開発の社会的背景
少子高齢化に伴う労働力不足は、全産業分野での社会課題である。素形材分野も例外ではなく、製造現場を支える中小企業において、技術・ノウハウの継承、人材育成が大きな課題となっている。そのような状況下、DX(デジタルトランスフォーメーション)への期待は大きく、ものづくりにおいてもスマートものづくりとして、デジタル化が進められている。しかしながら、素形材産業の各工程のうち生産に至る前の加工条件出しは、経験豊富な人材による、過去の経験と勘を頼りにした試行錯誤により行われ、デジタル化が積極的に進みにくい工程である。結果的に、加工の条件出しの工程がものづくり全体のDXのボトルネックになっているともいえる(図1)。
これまでにも、加工条件と成形物の特性をそれぞれ入力、出力としたAIモデルを構築した事例はあるものの、出力の予測にとどまっているのが現状である。結果として、最適加工条件を決めるには幾通りもの入力をモデルに与え、出力値が目標値とほぼ同じかどうかで判断せざるを得ず、人手不足の環境下において、実用的ではなかった。また、対象とする出力がただひとつの場合が多く、複数の要求仕様を同時に満足できていなかった。さらに、これまでのAIモデルでは膨大な学習データが必要であり、小規模生産現場において、そのデータを事前に準備する工程は現実的ではない。多品種変量生産への対応がさらに要求されていく中、少ない学習データで、複数の要求仕様を同時に満たし、最適加工条件を瞬時に決定する技術が望まれてきた。
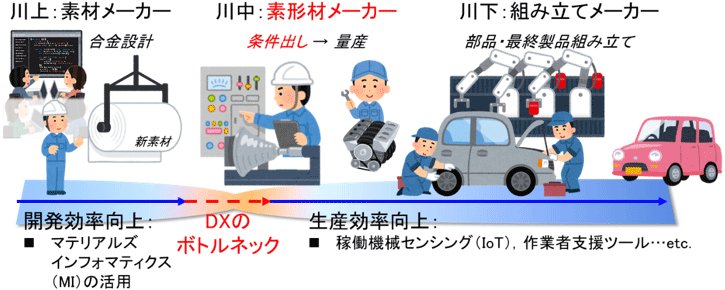
図1 ものづくり全体のDXに対する素形材産業でのボトルネックの状況
研究の経緯
産総研 製造技術研究部門では、少ない労働力で高付加価値を創製すること、社会・人々のニーズに臨機に応えた機能を提供することを目的に、IoT、AIを活用して得られたデータに基づき、能動的に設計、加工、評価を実施するものづくり技術の開発に取り組んできた。その一例として、スピニング加工技術を対象とした研究開発を行っている。
スピニング加工は回転する金属板にローラーを押し当てて逐次的に変形させる加工法である(図2)。これまで、製品の寸法はローラーパスや回転速度など多数の加工条件によって決まるという特徴を生かし、スピニング加工にロボット制御技術を活用することで、異形断面形状が成形できる新しいスピニング加工技術(3Dスピニング)を開発した(産総研 主な研究成果2008年9月29日)。また近年では、ローラーの柔軟な動きを介した組織制御による機能創製を目的に、材料組織学の観点からスピニング加工中の変形メカニズムの解明を進めている。このように、スピニング加工と他技術・学問の学際的なコラボレーションにより、スピニング加工の高度化を図ってきた。しかしながら、具体的な目標寸法となるように加工を行うには、何度も条件を変えて試作を行い、条件の修正と寸法変化の傾向について感覚をつかむ必要があり、多大な労力と時間がかかっていた。これらを軽減するために、加工条件と製品寸法の関係を捉えようとする研究がなされてきたが、多数の加工パラメータの影響を幅広く把握することができていなかった。このように、スピニング加工が抱える“加工条件出し時の試行錯誤への依存”は、依然として解決の難しい課題として残されてきた。
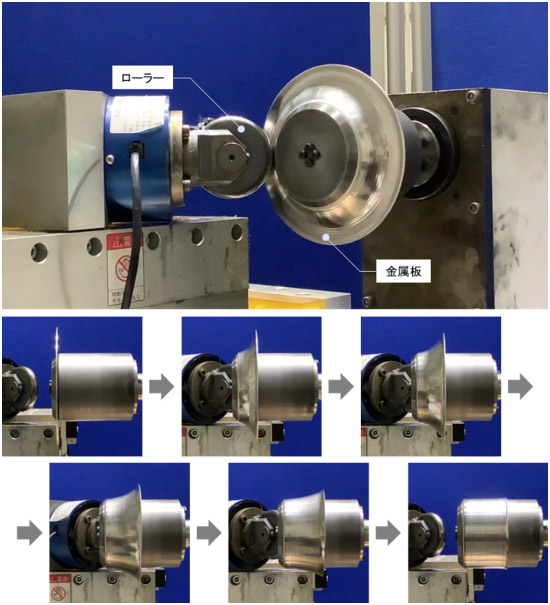
図2 スピニング加工の様子
今回、これを解決する手法としてAIに着目した。ただし、既往のAIを活用した加工技術開発との差別化として、中小企業などの小規模生産現場を念頭に、作業者が簡単に取り扱え、作業の支援となるAIツールの開発に焦点をおいた。具体的には、作業者が操作するパラメータを入力とし、観測対象(本研究では製品の複数箇所の板厚)を出力とするシンプルなモデルで入出力関係を表現することを前提とし、
- 少数のデータでモデルを構築できるようにする
- 最適化を行い、所望の板厚を実現する操作パラメータの具体値を出せるようにする
研究の内容
本研究では、35通りの条件下で金属板をカップ状に成形し、これら少数のデータを使って、加工中のローラーパスを入力層、実際に加工したカップの高さと高さ方向に3点の板厚を出力層とするニューラルネットワークモデルを構築した。このモデルから、反復解法と呼ばれる計算技法を用いて、目標とするカップの高さと板厚分布となる最適なローラーパスを求めた(図3)。モデルの構築に使ったデータのほとんどは高さ方向に板厚が一定ではなかったが、反復解法で求められたローラーパスで実際に加工すると、誤差0.1 mm以内で高さ方向の板厚分布が1.0 mm一定となるように成形できた(図4)。このように、複数の出力を同時に実現する最適な加工条件を瞬時に決定できる技術を開発し、一度の加工で狙い通りの製品寸法となるような成形を可能とした。
本技術は、膨大なデータを必要とせずに少数のデータを使ってモデルを構築し、構築したモデルに最適化を施して、所望の板厚を実現する操作パラメータの具体値を容易に算出する。“製造現場のDX”は一般に、加工技術とAIの両方について専門知識を有する人材の確保・育成をしなくてはならない、必要な機材の初期投資が高いなどの印象が持たれ、製造現場はDXの導入をためらう傾向にある。これに対し、本技術は手軽に低コストで製造現場、特に加工条件出し工程のDXを試みたいと考えている企業にとって、導入しやすく、その後の運用も含め取り扱いやすい、汎用性の高い作業支援AIツールとなる。
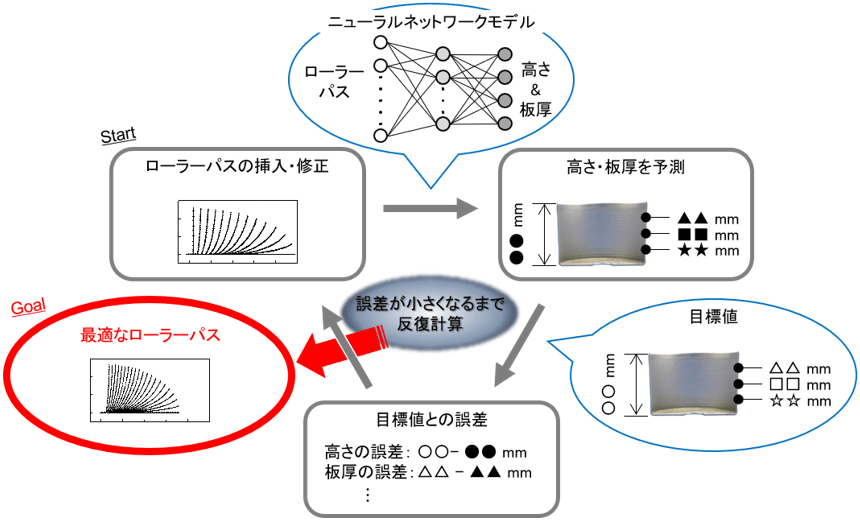
図3 本手法における最適ローラーパスが求まるまでの流れ
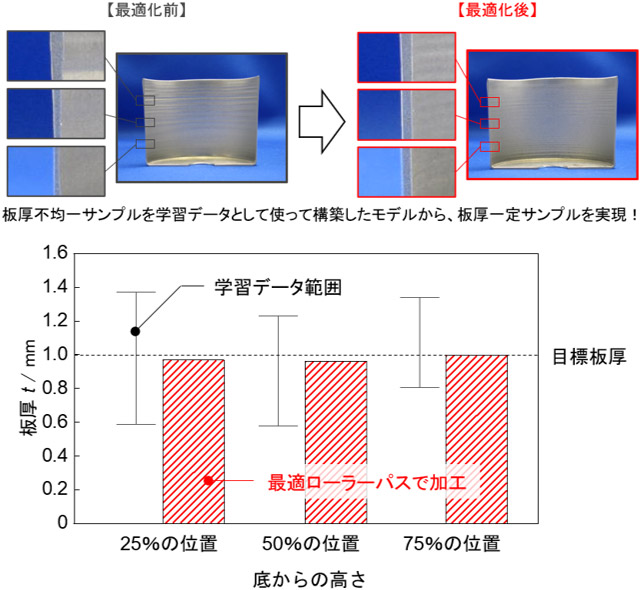
図4 決定した最適ローラーパスによる板厚一定の実現
今後の予定
スピニング加工において取り扱う素材や金型の寸法、材質を拡張しながら、目標形状やローラーパスの複雑化に対応した、柔軟なモデルの開発を引き続き行う。同時に製造現場での実装を試み、より製造現場に寄り添うモデル開発を行う。また、本成果は、スピニング加工のみならずその他の素形材加工技術にも原理的に応用可能である。産学官の連携により本成果を他の加工法へ適用し、データ駆動型ものづくりを展開していく。手軽に低コストで加工条件出し工程のDXを試みたいと考えている企業の支援を積極的に行っていきたい。
用語の説明
- 塑性加工
- 光の波長以下の周期を持つナノ構造により光の反射率を低減できる構造体。広い入射角範囲、広い波長帯域で反射率を低減できるため、太陽電池やディスプレー、レンズなどの光学部品への応用が期待されている。[参照元へ戻る]
- ニューラルネットワーク
- 曇りを防ぐ機能。材料表面の親水・撥水処理などにより防曇機能を付与できる。親水処理によって防曇機能を付与するには、超親水表面(10度以下の水接触角)とすることが有効で、超親水表面では、水滴が生成される前に水膜化するため防曇機能を発揮できる。[参照元へ戻る]
- 反復解法
- 光の波長以下の周期を持つ構造体。ここでは、おおよそ200nmの間隔を持つ構造体。[参照元へ戻る]
- DX(デジタルトランスフォーメーション)
- 軟化させたプラスチックを、圧力(射出圧という。10〜3000kgf/cm2)をかけて金型に充填して、プラスチックの成形を行う方法。[参照元へ戻る]